Quantas são as formas de imprimir em 3D?
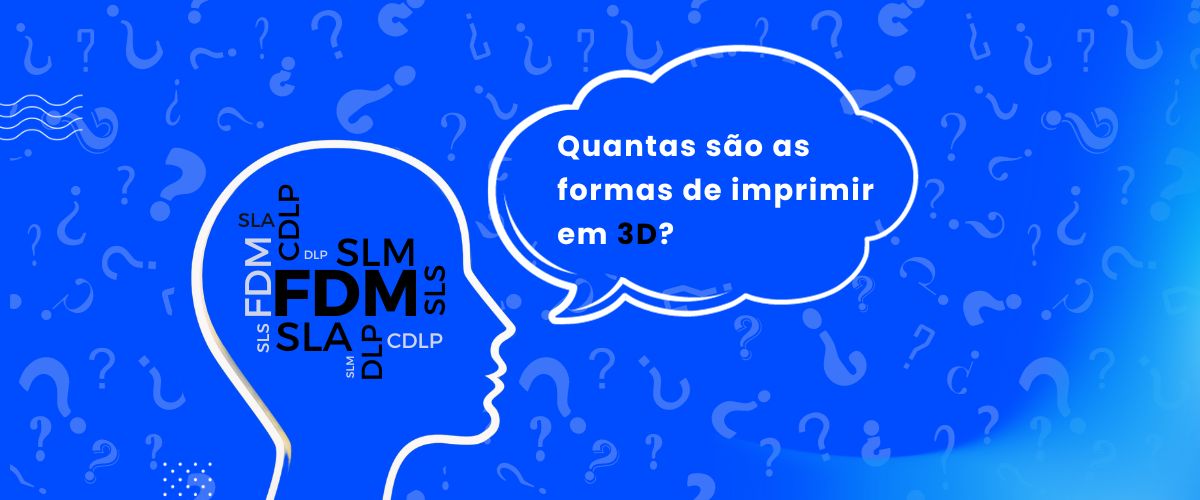
Já falamos em nossa primeira coluna sobre o surgimento da impressão 3D, do nascimento da manufatura aditiva em 1984 com Chuck Hull, da primeira venda de um sistema de prototipagem rápida em 1986, o surgimento de uma era ao redor da máquina a laser que endurece uma resina líquida, a SLA – Stereolitographic Apparatus, até a revolução decorrente da queda das patentes, a era das impressoras autorreplicáveis, as RepRaps, em 2009, que trouxeram o termo popular “Impressão 3D” e o termo sofisticado e acadêmico, “Manufatura Aditiva.”
Mas afinal, quantas formas de se imprimir em 3D existem, já que só nesse primeiro parágrafo mencionei aquela que utiliza laser, e todos nós conhecemos alguma que usa um fio de plástico, não é mesmo? Olha, são muitas.
Na corrida pela tecnologia de impressão em 3D, diversas empresas criaram formas variadas de solidificar matéria, seja para escapar de uma patente de uma empresa concorrente ou para agregar alguma característica que ainda não havia no mercado.
Um dos institutos mais prestigiados do mundo, a HUBS, delineou esse cenário, mostrando como cada processo deu origem a diferentes empresas do segmento.
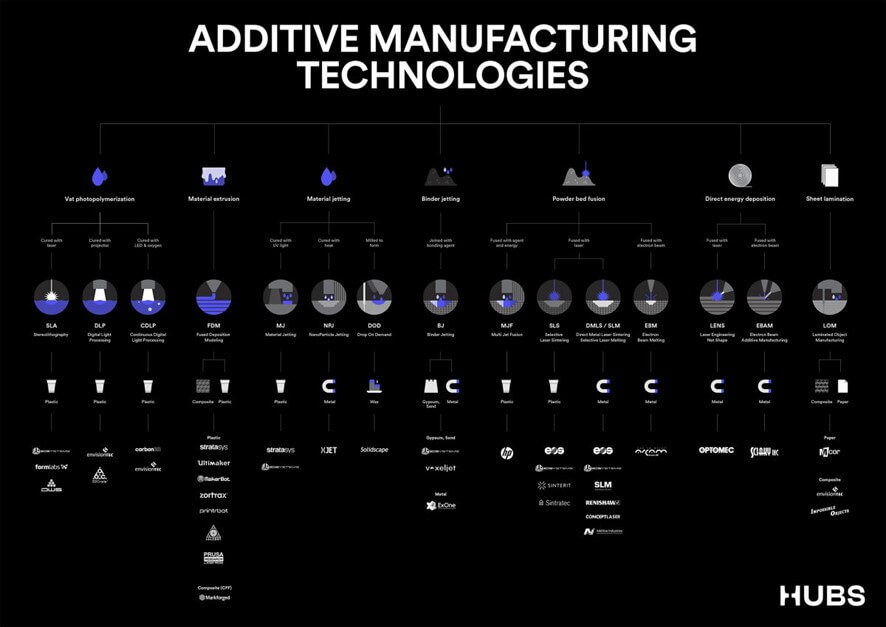
(acesse esse poster em alta resolução acessando: Additive manufacturing technologies poster | Hubs)
Para entendermos esse gráfico, vamos simplificar um pouco os processos e nos ater àqueles que usamos em nossa comunidade:
Impressão 3D por luz:
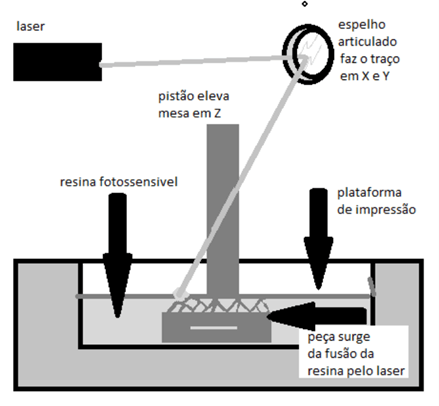
SLA, DLP e MJP são todos processos que partem de uma resina líquida e, através da luz, a resina é endurecida, formando a peça. A impressão 3D pode ocorrer em uma bandeja perfurada, que gradualmente mergulha em um volume cheio dessa resina. Cada vez que a bandeja submerge na resina, o laser endurece aquela lâmina exata de material que ficou sobre a resina já curada. Esse é o processo pioneiro de impressão 3D, chamado SLA, e geralmente envolve o laser como fonte de luz.
Conforme ocorreu a queda das patentes, alguém percebeu que a SLA, apesar das vantagens de produzir as peças com o melhor acabamento diretamente da impressora, já que a lâmina de resina pode ser tão fina quanto 0,05mm, geralmente o custo para encher um tonel de resina líquida era muito alto.
Foi quando um jovem chamado Mike Lobovsky teve a ideia, e se a bandeja com o material curado, em vez de submergir na resina, se afastasse dela?
Ele usou um laser desses de leitura de DVD e CD em drivers de computador, e um braço que se afastava não mais do que um balde cheio de resina, mas de um prato de sopa com alguma resina líquida ali colocada.
Nasciam as impressões que podem ser chamadas de DLP – Digital Light Process, mas também são chamadas de SLA ou LED, quando em vez de laser, usamos uma tela de celular ou tablet para emitir a luz. Se trocarmos a resina líquida por pós de plástico, o processo passa a ser chamado de SLS – Sinterização por Laser Seletivo.
E se os pós forem de metal, chamamos o processo de DMT – Direct Metal Technology. Em comum, todos os processos utilizam o laser ou luz UV em diferentes fontes para curar ou fundir a matéria-prima. Se for líquida, há uma cura, se for pó, há uma sinterização.
Impressão 3D por plásticos
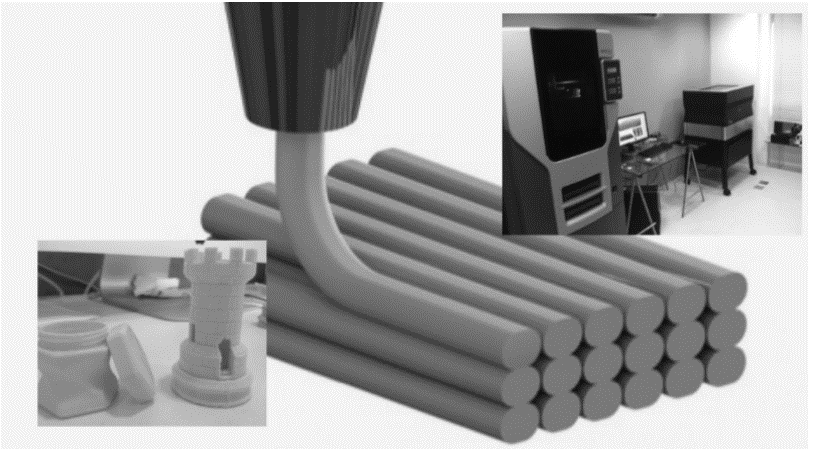
“A impressão 3D por fios de plástico nasceu em 1988, criada pelo norte-americano Scott Crumb, fundador da Stratasys.
Este meio de impressão tornou-se o mais popular do mundo por diversos motivos: os plásticos, diferentes das resinas fotossensíveis, possuem dados de engenharia conhecidos, tais como resistência à torção, flambagem, impacto, módulo de elasticidade, entre outros.
Plásticos são fáceis de armazenar, não endurecem apenas por exposição ao sol, não criam cristais que podem interferir no acabamento das peças e não requerem materiais de segurança como luvas, óculos ou máscaras para lidar com a matéria-prima.
Não por acaso, de acordo com uma pesquisa da HUBS, esse é o processo mais popular de impressão 3D do mundo, o processo por fio, batizado por Scott Crumb de FDM – Fused Deposition Modeling – ou Modelagem por Deposição de Fundido em português.
A comunidade decidiu dar o nome de FFF – Fabricação por Filamento Fundido, já que FDM é supostamente uma patente da Stratasys, mas o fato é que todo mundo usa FDM.
Outra das vantagens é que plásticos já têm sido usados com muito sucesso na engenharia desde os anos de 1960 e 1970, quando houve uma explosão de seu uso em bens de consumo, linha branca, e gradualmente o material encontrou seu caminho para os automóveis, indo desde os parachoques até o painel, e agora, com a transição dos motores à explosão para elétricos, fazendo parte dos módulos de tração dos veículos.
Mas isso não quer dizer que a impressão por plásticos é perfeita. Longe disso: ela tem o pior acabamento de longe entre todos os meios de impressão 3D conhecidos até agora, mas, por outro lado, como quaisquer outros plásticos, é possível dar acabamento, lixar, aplicar pintura veicular, massa plástica, entre outras formas.”
Em síntese:
Existem mais de 30 patentes de como fazer uma camada de material aderir à outra. Dependendo do material em questão, isso pode ser feito por luz, sinterização ou simplesmente fusão, como as impressoras de plásticos. Na nossa comunidade maker, dividimos o mercado em duas grandes vertentes: as impressoras de resina (resinas líquidas, fotossensíveis) e as impressoras de plástico (por fio, geralmente vendidas em carretéis), mas essa é apenas uma fração de todas as formas que existem.
Impressão por Luz, vantagens:
- Acabamento direto na impressão;
- Velocidade de impressão para múltiplos objetos;
- Vasta aplicação onde a precisão precisa ser absoluta, como em medicina, odontologia ou objetos colecionáveis e maquetaria.
Desvantagens:
- Propriedades mecânicas fracas;
- Custo das resinas;
- Cuidados com a matéria-prima.
Impressão por fio de plástico, vantagens:
- Diversos polímeros conhecidos na engenharia: ABS, Policarbonato, Nylon, etc.;
- Baixo custo de armazenamento da matéria-prima;
- Simplicidade de uso e aplicação da peça impressa.
Desvantagens:
- Acabamento direto na impressora é baixo;
- Tempo de impressão 3D longo para múltiplos objetos;
- Uso de materiais extras para apoiar peças complexas.